Thermographic Testing/Survey
What is Thermographic Testing and Why is it Crucial?
Thermographic Testing, commonly referred to as infrared inspection, serves as a non-intrusive predictive maintenance technique. It is specifically designed to identify defects in connections, system overloads, compromised insulation, and various other issues in electrical systems.
By employing infrared thermography, Thermographic Testing helps pinpoint areas of excessive heat, thereby enabling timely interventions. This prevents unnecessary power consumption, escalating maintenance expenses, service disruptions, catastrophic equipment breakdowns, and potential damage to machinery.
How Does Thermographic Testing Function?
The core of Thermographic Testing lies in its advanced infrared visual scanning technology. During a Thermographic Testing scan, a specialised thermal camera captures heat traces that are invisible to the naked eye. This technology allows inspectors to effortlessly spot heat irregularities, which are color-coded in the thermal image for easy identification.
The Importance of Thermographic Testing
Electrical systems are composed of numerous connections and components that offer resistance to the flowing current. Over time, these elements degrade, leading to increased resistance and localised heat spikes. Whether it’s an aging connection or a substandard component, these heat concentrations can result in both energy wastage and equipment failure. Thermographic Testing can proactively identify these temperature spikes, enabling preemptive action before the issue escalates into a significant problem.
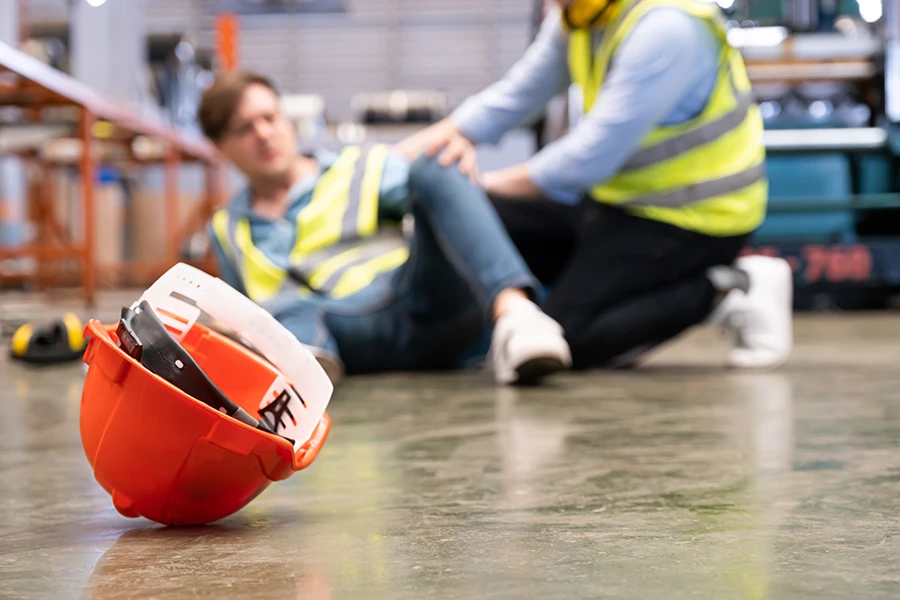
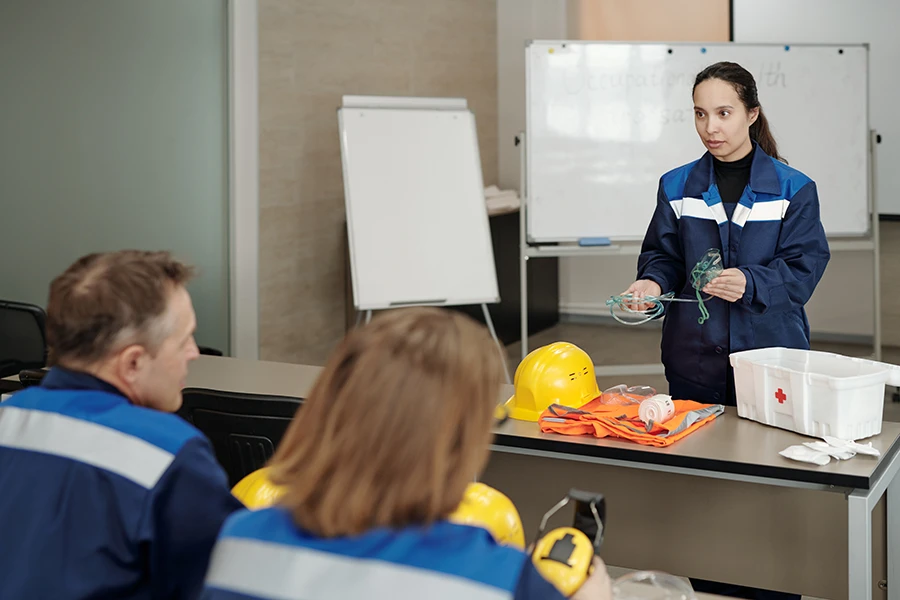
Is Thermographic Testing a Necessity?
The risks tied to electrical equipment failure are manifold, ranging from financial burdens to severe safety hazards. According to the National Fire Protection Association (NFPA), approximately 10% of fires in manufacturing facilities are attributed to electrical system failures. Moreover, faulty components and connections can expose workers to live electrical circuits, posing a risk of electrocution. Thermographic Testing serves as a predictive maintenance tool that can mitigate these risks well in advance.
Identifying the Need for Thermographic Testing in Your Facility
Facilities with energised electrical systems are prime candidates for predictive maintenance services like Thermographic Testing. This is especially true for commercial setups with high power consumption, heavy machinery, and intricate electrical distribution systems. Such facilities are at an elevated risk of expensive failures and would substantially benefit from annual Thermographic Testing scans.
Additional Indicators for Thermographic Testing:
- A noticeable uptick in energy usage without corresponding equipment activity
- Experiencing equipment slowdowns
- Unexplained power surges occurring
- Dimming lights upon equipment startup
- Machinery operating at higher temperatures than usual
- Recent addition of equipment or repairs that have increased electrical demand
By incorporating Thermographic Testing into your maintenance routine, you can significantly reduce risks and optimise operational efficiency.
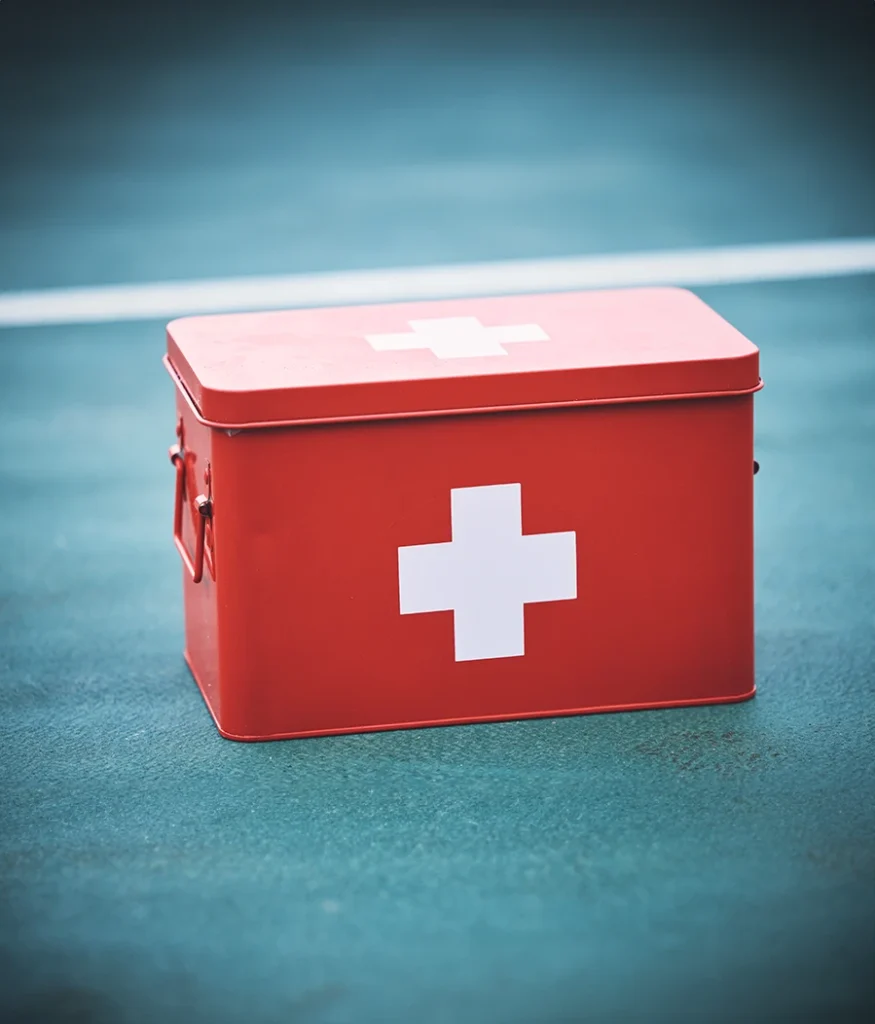